Motorized Pitch and Yaw Platform
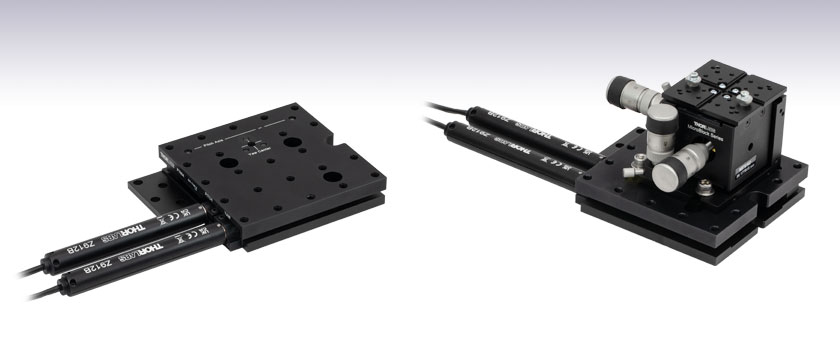
- Low Profile: 25 mm (0.98") Platform Height
- ±2.5° Pitch and ±4.0° Yaw
- Load Capacity: 2.0 kg (4.4 lbs)
- DC Servo Actuators
PY004Z9
High-Load Pitch and Yaw Stage with DC Servo Actuators
Application Idea
3-Axis Flexure Stage Mounted Directly to a PY004Z9 High-Load Pitch and Yaw Stage for High-Precision 5-Axis Control

Please Wait
Key Specificationsa | ||
---|---|---|
Adjustment Range | Pitch: ±2.5° Yaw: ±4.0° |
|
Minimum Achievable Incremental Movement |
Pitch: 7.13 arcsec Yaw: 15.71 arcsec |
|
Bidirectional Repeatability | Pitch: 27.85 arcsec Yaw: 4.75 arcsec |
|
Crosstalk | <0.05° (3 arcmin) | |
Maximum Horizontal Load Capacitya,b |
2.0 kg (4.4 lbs) | |
Maximum Vertical Load Capacityc |
Load Distance from Top Platform |
Max Load |
30.0 mm (1.18") | 1.8 kg (4.0 lbs) | |
50.0 mm (1.97") | 1.1 kg (2.4 lbs) | |
80.0 mm (3.15") | 0.7 kg (1.5 lbs) | |
Deck Height | 25.0 mm (0.98") | |
Bushing Diameter | 9.5 mm (3/8") | |
Included Drives | Z912Bd DC Servo Motors (Qty. 2) |

Click to Enlarge
Figure 1.1 K-Cube® DC Servo Motor Controller (Two Required)
Features
- Motorized Pitch and Yaw Adjustment via Included DC Servo Actuators
- Twenty-Four 1/4"-20 (M6) Tapped Holes with 1.00" (25.0 mm) Spacing
- Cobine with Linear Stages to Add Rotational Degrees of Freedom
- 0.98" (25.0 mm) Deck Height
- Black-Anodized Aluminum Construction
This Motorized Pitch and Yaw Platform provides ±2.5° of adjustment in pitch and ±4.0° in yaw. It is designed for use with loads up to 4.4 lbs (2.0 kg), such as lasers, cameras, and 3-axis stages. The actual maximum load will depend on the positioning of the load on the platform (see the Specs tab for more details). The 4.41" x 4.53" (112.0 mm x 115.0 mm) top platform is equipped with an array of twenty-four 1/4"-20 (M6) threaded mounting holes on 1.00" (25.0 mm) centers.
The base of the pitch and yaw platform is provided with eight through holes for attachment to imperial or metric optical tables and breadboards. The through holes allow the tapped holes on the unit to be in line with the optical table hole pattern or midway off the optical table hole pattern. The unit can also be secured at any arbitrary position by using two CL6 table clamps (sold separately).
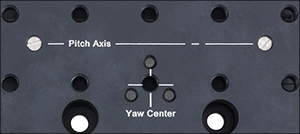
Click to Enlarge
Figure 1.2 Engravings on the platform indicate the pitch axis and yaw center to help minimize crosstalk.
Included and Compatible Actuators
The two included Z912B DC servo actuators feature a 1.6' (485 mm) cable length. They provide a minimum achievable incremental movement of 7.13 arcseconds in pitch and 15.71 arcseconds in yaw. The actuators attach to the stage using a flexure clamp that tightens around the Ø3/8" (Ø9.5 mm) barrel. If desired, the Z912B actuator can be replaced by any manual or motorized actuator that includes a Ø3/8" (Ø9.5 mm) barrel, including stepper motor actuators and manual micrometers.
Controller Options
Thorlabs recommends using two KDC101 DC Servo Controllers (available below); one for each axis. The latest version of the Kinesis software can be downloaded here. Firmware version 2.2.8 or higher and Kinesis software version 1.14.44 or higher are required for using the KDC101 with the PY004Z9(/M) platforms. Please see the Kinesis Software and Kinesis Tutorial tabs for details.
PY004Z9(/M) Specifications
Specification | Value | |
---|---|---|
Pitch and Yaw Adjustment | ||
Adjustment Range | Pitch: ±2.5° Yaw: ±4.0° |
|
Minimum Achievable Incremental Movement |
Pitch: 7.13 arcsec Yaw: 15.71 arcsec |
|
Bidirectional Repeatability | Pitch: 27.85 arcsec Yaw: 4.75 arcsec |
|
Maximum Velocity | Pitch: 3600 arcsec/s Yaw: 3600 arcsec/s |
|
Maximum Acceleration | Pitch: 3600 arcsec/s2 Yaw: 3600 arcsec/s2 |
|
Crosstalk | <0.05° (3 arcmin) | |
Stage | ||
Maximum Horizontal Load Capacitya,b | 2.0 kg (4.4 lbs) | |
Maximum Vertical Load Capacityc | Load Distance from Top Platform |
Max Load |
30.0 mm (1.18") | 1.8 kg (4.0 lbs) | |
50.0 mm (1.97") | 1.1 kg (2.4 lbs) | |
80.0 mm (3.15") | 0.7 kg (1.5 lbs) | |
Deck Height | 25.0 mm (0.98") | |
Bushing Diameter | 9.5 mm (3/8") | |
Body Construction | Black-Anodized Aluminum | |
Actuator | ||
Included Drives | Z912Bd (Qty. 2) | |
Motor Type | DC Servo Motor | |
Maximum Phase to Phase Resistance | 33.0 Ω | |
Maximum Phase to Phase Inductance | 0.6 mH | |
Operating Temperature Range | 41° to 104° F (5° to 40° C) |
|
Cable Length | 485.0 mm (19.09") | |
Connector | D-Type Male | |
Compatible Controller | KDC101 | |
Physical | ||
Dimensions (L x W x H)e | 9.19" x 4.53" x 0.98" (233.3 mm x 115.0 mm x 25.0 mm") |
|
Weight | 0.87 kg (1.91 lbs) |
Horizontal Load Capacity Diagram
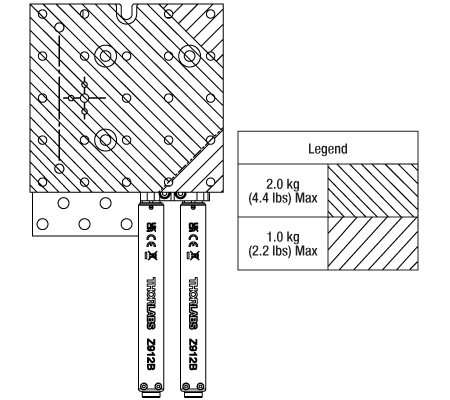
Click to Enlarge
Figure 2.1 Diagram Showing Areas of Different Maximum Load Capacity
for the PY004Z9(/M) Stage
Z912B Connector Pin Out
D-Type Male
Pin | Description | Pin | Description |
---|---|---|---|
1 | Ground (Limit and Vcc) | 9 | Resistive Identification |
2 | Forward Limit | 10 | +5 VDC |
3 | Reverse Limit | 11 | Encoder Channel A |
4 | Reserved for Future Use | 12 | Reserved for Future Use |
5 | Motor (-) | 13 | Encoder Channel B |
6 | Reserved for Future Use | 14 | Pin 2 Ident EEPROM |
7 | Motor (+) | 15 | Pin 1 Ident EEPROM |
8 | Reserved for Future Use |
Software
Kinesis Version 1.14.53
The Kinesis Software Package, which includes a GUI for control of Thorlabs' Kinesis system controllers.
Also Available:
- Communications Protocol
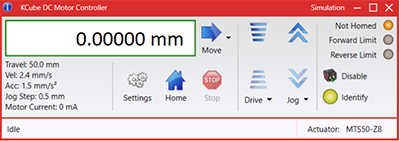
Figure 58A Kinesis GUI Screen
Thorlabs offers the Kinesis® software package to drive our wide range of motion controllers. The software can be used to control devices in the Kinesis family, which covers a wide variety of motion controllers ranging from small, low-powered, single-channel drivers (such as the K-Cubes®) to high-power, multi-channel benchtop units and modular 19" rack nanopositioning systems (the MMR60x Rack System).
The Kinesis Software features .NET controls which can be used by 3rd party developers working in the latest C#, Visual Basic, LabVIEW™, or any .NET compatible languages to create custom applications. Low-level DLL libraries are included for applications not expected to use the .NET framework and APIs are included with each install. A Central Sequence Manager supports integration and synchronization of all Thorlabs motion control hardware.
By providing this common software platform, Thorlabs has ensured that users can mix and match any of our motion control devices in a single application, while only having to learn a single set of software tools. In this way, it is perfectly feasible to combine any of the controllers from single-axis to multi-axis systems and control all from a single, PC-based unified software interface.
The software package allows two methods of usage: graphical user interface (GUI) utilities for direct interaction with and control of the controllers 'out of the box', and a set of programming interfaces that allow custom-integrated positioning and alignment solutions to be easily programmed in the development language of choice.
Thorlabs' Kinesis® software features new .NET controls which can be used by third-party developers working in the latest C#, Visual Basic, LabVIEW™, or any .NET compatible languages to create custom applications.
C#
This programming language is designed to allow multiple programming paradigms, or languages, to be used, thus allowing for complex problems to be solved in an easy or efficient manner. It encompasses typing, imperative, declarative, functional, generic, object-oriented, and component-oriented programming. By providing functionality with this common software platform, Thorlabs has ensured that users can easily mix and match any of the Kinesis controllers in a single application, while only having to learn a single set of software tools. In this way, it is perfectly feasible to combine any of the controllers from the low-powered, single-axis to the high-powered, multi-axis systems and control all from a single, PC-based unified software interface.
The Kinesis System Software allows two methods of usage: graphical user interface (GUI) utilities for direct interaction and control of the controllers 'out of the box', and a set of programming interfaces that allow custom-integrated positioning and alignment solutions to be easily programmed in the development language of choice.
For a collection of example projects that can be compiled and run to demonstrate the different ways in which developers can build on the Kinesis motion control libraries, click on the links below. Please note that a separate integrated development environment (IDE) (e.g., Microsoft Visual Studio) will be required to execute the Quick Start examples. The C# example projects can be executed using the included .NET controls in the Kinesis software package (see the Kinesis Software tab for details).
![]() |
Click Here for the Kinesis with C# Quick Start Guide Click Here for C# Example Projects Click Here for Quick Start Device Control Examples |
![]() |
LabVIEW
LabVIEW can be used to communicate with any Kinesis-based controller via .NET controls. In LabVIEW, you build a user interface, known as a front panel, with a set of tools and objects and then add code using graphical representations of functions to control the front panel objects. The LabVIEW tutorial, provided below, provides some information on using the .NET controls to create control GUIs for Kinesis-driven devices within LabVIEW. It includes an overview with basic information about using controllers in LabVIEW and explains the setup procedure that needs to be completed before using a LabVIEW GUI to operate a device.
![]() |
Click Here to View the LabVIEW Guide Click Here to View the Kinesis with LabVIEW Overview Page |
![]() |
Posted Comments: | |
user
 (posted 2025-01-23 09:13:29.95) Is there a possibility that the motorized pitch and yaw stage moves in degrees using the K-Cube. We are not sure how to convert the mm we see on the Kinesis GUI to angle? Could you please help with that? tschofield
 (posted 2025-01-31 10:25:51.0) Thank you for reaching out. Under ‘Actuator’ in the bottom right of the red box in Kinesis GUI, you can select PY004Z9(/M) Pitch/Yaw. This will change the units in the Kinesis GUI to the more appropriate angle in degrees rather than distance in mm. Jesse Ahlquist
 (posted 2022-09-02 09:52:07.84) Hi,
This product is great; however, something we came across in a recent design review for our specific application is whether the motorized actuators must mount in this specific orientation with respect to stage movement.
More specifically - our application would benefit from the pitch and raw actuators ability to mount vertically such that they are perpendicular rather than parallel with the pitch axis.
Is something like this a possibility? Perhaps there is an alternative product which satisfies this need?
Thanks!
Jesse cwright
 (posted 2022-09-06 10:51:33.0) Response from Charles at Thorlabs: Thank you for contacting us. We are happy you have found the product useful and welcome the feedback. Unfortunately it is not possible to adapt this stage such that the adaptors are vertical and we do not currently have another stage which could serve as an alternative with this configuration. chf7
 (posted 2018-09-18 14:17:29.77) Is this product vacuum compatible? AManickavasagam
 (posted 2018-09-19 04:40:01.0) Response from Arunthathi @ Thorlabs: Thanks for your query. PY004Z8 is not vacuum compatible as the stage is made of Aluminium and it is anodised. Also, the grease used is not suitable to use in vacuum conditions. |

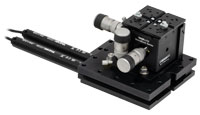
Click to Enlarge
Figure G1.1 Mounting a 3-axis positioner on the PY004Z9 platform results in precision 5-axis control useful in many applications such as fiber alignment.
- DC Servo Actuator Provides a Large Adjustment Range:
- Pitch: ±2.5°
- Yaw: ±4.0°
- Maximum Load Capacity: 2.0 kg (4.40 lbs)
- Controllers and Power Supplies Sold Separately
Thorlabs' PY004Z9(/M) Motorized Pitch and Yaw Platform provides an adjustment range of ±2.5° and ±4.0° in pitch and yaw, respectively. An array of twenty-four 1/4"-20 (M6) tapped holes allows easy integration with a wide variety of common optomechanical setups. The stage features a maximum load capacity of 2.0 kg (4.40 lbs), making it ideal for use with lasers, cameras, or 3-axis platforms. The stage requires two controller units and power supplies to operate. For this purpose, we recommend our KDC101

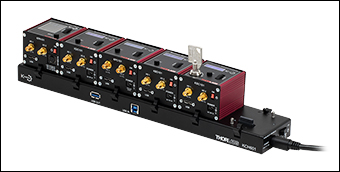
KCH601 USB Controller Hub (Sold Separately) with Installed K-Cube® Modules
- Front Panel Velocity Wheel and Digital Display for Controlling Motorized Stages or Actuators
- Two Bidirectional Trigger Ports to Read or Control External Equipment
- Interfaces with Computer Using Included USB Cable
- Fully Compatible with Kinesis Software Package
- Compact Footprint: 60.0 mm x 60.0 mm x 49.2 mm (2.42" x 2.42" x 1.94")
- Power Supply Not Included (See Below)
Thorlabs' KDC101 K-Cube® Brushed DC Motor Controller provides local and computerized control of a single motor axis. It features a top-mounted control panel with a velocity wheel that supports four-speed bidirectional control with forward and reverse jogging as well as position presets. A backlit digital display is also included that can have the backlit dimmed or turned off using the top-panel menu options. The front of the unit contains two bidirectional trigger ports that can be used to read a 5 V external logic signal or output a 5 V logic signal to control external equipment. Each port can be independently configured.
The unit is fully compatible with our Kinesis software package. Please note that while the KDC101 controller is also fully supported by our XA software suite, the PY004Z9(/M) stage is not supported at this time, so the Kinesis software package should be used. A full list of products supported by XA can be found here. Please see the Kinesis Software tab for more information.
Please note that this controller does not ship with a power supply. Compatible power supplies are listed below. Additional information can be found on the main KDC101 DC Servo Motor Controller page.

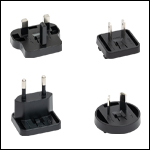
Click for Details
Figure 780B Each KPS201 power supply includes one region-specific adapter, which can be selected upon checkout.
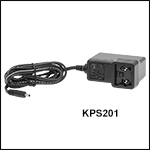
Click to Enlarge
Figure 780A The KPS201 Power Supply Unit
- Individual Power Supply
- KPS201: For K-Cubes® or T-Cubes™ with 3.5 mm Jacks
- USB Controller Hubs Provide Power and Communications
- KCH301: For Up to Three K-Cubes or T-Cubes
- KCH601: For Up to Six K-Cubes or T-Cubes
The KPS201 power supply outputs +15 VDC at up to 2.66 A and can power a single K-Cube or T-Cube with a 3.5 mm jack. It plugs into a standard wall outlet.
The KCH301 and KCH601 USB Controller Hubs each consist of two parts: the hub, which can support up to three (KCH301) or six (KCH601) K-Cubes or T-Cubes, and a power supply that plugs into a standard wall outlet. The hub draws a maximum current of 10 A; please verify that the cubes being used do not require a total current of more than 10 A. In addition, the hub provides USB connectivity to any docked K-Cube or T-Cube through a single USB connection.
For more information on the USB Controller Hubs, see the full web presentation.